Geprüfte SicherheitIEF-Werner: Palettieranlage aus Be- und Entladesystem schafft sichere Montagevoraussetzungen
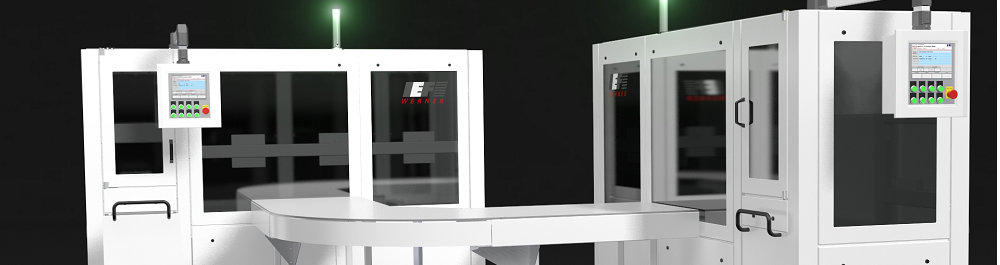
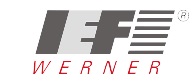
IEF-Werner entwickelt für Kunden individuelle Lösungen – zum Beispiel ein Palettiersystem, das aus einem Be- und einem Entladesystem besteht. Das Besondere: Über RFID-Tags werden die Trays, über Barcode die darin befindlichen Produkte mit einem MES-System abgeglichen. Dies stellt sicher, dass bei verschiedenen Produkten immer die richtigen Teile dem Prozess zu- und abgeführt werden. Zwischenablagen, fehlerhafte Produkte und leere Trays puffert die Maschine, um sie für den verketteten Vorgang bereitzustellen – eine wirtschaftliche Lösung, die ein Anwender bereits erfolgreich einsetzt.
Eine schnelle und zuverlässige automatisierte Be- und Entladung von Produkten aus Ladungsträgern für die Montage von Baugruppen spielt in vielen Betrieben in der Automobil-, Pharma-, Elektronik- oder Medizintechnik eine große Rolle. So können Firmen wirtschaftlich arbeiten – insbesondere in der Serienfertigung hoher Stückzahlen. Mit leistungsstarken Palettierlösungen erreichen Anwender bei ihren Prozessen eine hohe Effizienz. Ebenso stellen sie die Bereitstellung der Bauteile sicher, da keine manuellen Fehler auftreten können. Die IEF-Werner GmbH bietet Palettiersysteme und legt dabei viel Wert auf kurze Taktzeiten und hohe Zuverlässigkeit. Auf individuelle Vorgaben gehen die Ingenieure mit ihren Anlagen explizit ein. „Wir haben für einen Kunden eine äußerst wirtschaftliche Lösung entwickelt, die aus einem Be- und Entladesystem besteht“, berichtet Stefan Deck, Geschäftsführer bei IEF-Werner. In dieser konkreten Anwendung sollten plattenförmige Produkte mit den Maßen 310 x 410 Millimeter und Stärken von 0,1 bis 1,5 Millimetern aus Trays entnommen und für die weitere Verarbeitung einer Fördertechnik zugeführt werden. Die Platten bestehen aus Aluminium oder aus Kupferlegierungen und besitzen verschiedene Strukturen. Damit sind sie auch unterschiedlich schwer. „Wir haben also verschiedene Produkte, die von der Anlage je nach Auftrag sicher gehandhabt und erkannt werden müssen“, erklärt Deck.
Sicherheit steht ganz oben
Bis zu zehn in Form, Material und Gewicht gleiche Platten befinden sich jeweils in einem Kunststoff-Tray. Damit die Produkte nicht zusammenhaften, liegen Zwischenlagen aus antihaftbeschichtetem Kunststoff dazwischen. „Die Aufgabe bestand nun darin, die Produkte zu vereinzeln, lagerichtig aus den Trays sowie dem Prozess zu entnehmen, auf Richtigkeit zu prüfen und der weiteren Verarbeitung zuzuführen“, beschreibt Deck.
Der Bediener nimmt einen Wagen, auf dem mehrere beladene Kunststoff-Trays gestapelt sind, und schiebt ihn in das Beladesystem. Beladen wiegen die Wagen bis zu 150 Kilogramm. Damit der Fertigung die richtigen Produkte zugeführt werden, ist jeder Tray mit einem RFID-Tag versehen. Es sollten sich in jedem Ladungsträger auch nur sortenreine Produkte befinden – „aber sich ganz sicher sein kann man da eben nicht“, sagt Deck. Deshalb ist auf jeder Platte ein Barcode auf der Ober- und/oder Unterseite aufgedruckt, der nach der Entnahme aus dem Tray gescannt wird.
Die Hubachse nimmt mit ihrem adaptierten Palettengreifer das oberste Tray aus dem Wagen und fährt damit zu einem Transponder, der den RFID-Tag liest. Stimmen die Daten, entnimmt die Handlingeinheit das oberste Produkt aus dem Tray. Ein Scanner liest den Barcode, Sensoren messen zusätzlich die Dicke. Die Daten gleicht die Anlage mit dem Auftrag im betreiberseitigen Manufacturing Execution System (MES) ab. Danach legt die Handlingeinheit die Platte auf das Transportband. Falls notwendig wird dieses dabei gedreht. Was aber, wenn die Infos auf dem Barcode nicht mit den Daten im System übereinstimmen? „Dann erfolgt ein Signal wie auch eine Warnmeldung an das Bedienpersonal mit entsprechender Aufforderung zum manuellen Eingriff und zur Überprüfung. Damit die Zwischenlagen nicht am Produkt haften bleiben, erfolgt während dem Entnehmen aus dem Tray parallel ein Luftimpuls aus einem Abblasrohr. Diese Zwischenablagen transportiert der Greifer dann in den dafür vorgesehenen Speicher, die leeren Trays in dessen Pufferspeicher.
„Die Vorteile dieses Konzepts zeigen sich besonders bei verketteten Anlagen und Prozess-Schritten“, sagt Deck. „Denn gerade hier müssen die richtigen Komponenten schnell und präzise bereitgestellt werden, damit sie anschließend in vorgegebener Lage den weiteren Bearbeitungsschritten zu- und abgeführt werden können.“ Mit dieser Lösung ermöglicht IEF-Werner eine effiziente Produktionsautomatisierung, die ja immer mehr zum entscheidenden Wettbewerbsfaktor wird.
Quelle: www.ief.de
Foto „head“: Mit der Anwendung werden plattenförmige Produkte aus Trays entnommen und für die weitere Verarbeitung einer Fördertechnik zugeführt.